
Manufacturing Tech | How to choose the right hardware mix
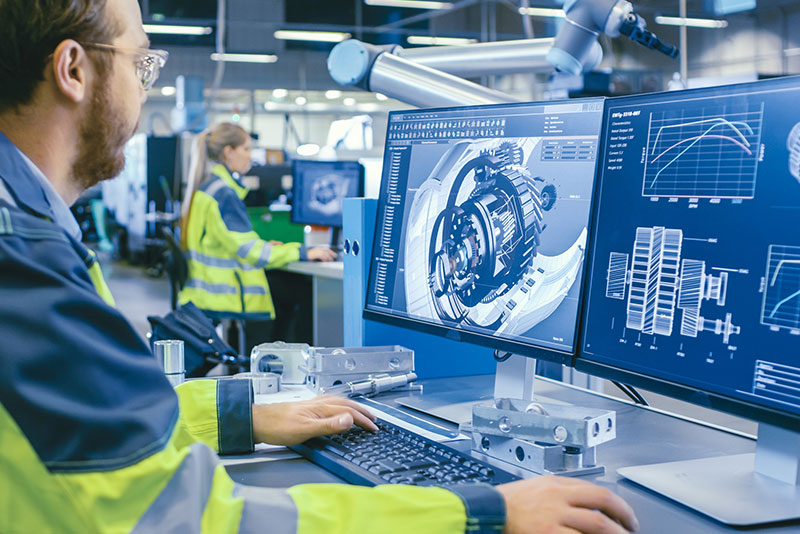
When it comes to software, as a manufacturing business, you likely run some CAD software for your designers, some ERP software and a QMS.
But what sort of hardware is right for you?
There are so many choices, and it can all get overwhelming. Choosing a mix of hardware is the answer. But making sure it’s the right mix is the real key to making the technology in your manufacturing business work at its best.
To help you get started with finding the right mix, I’ve answered the most common questions we get about hardware for manufacturers.
#1 – What’s the best hardware for CAD (Computer Aided Design) Systems?
Your designers probably use something like AutoCAD or REVIT, both from AutoDESK. Choosing the best hardware that’s optimised for these programs isn’t as simple as ordering a computer for reception.
Your typical office workstation won’t cut it. Or if it does, it won’t cut it very well, especially when it comes to 3D design.
For most 2D and 3D design, you need a computer that’s optimised for the process, and one of the key things that gets overlooked is the graphics card.
The graphics card or VGA card needs to be optimised for CAD design. If we’re talking about 3D, then a base level card is not a good solution.
Nvidia Quadro and AMD FirePro are the two most common options, with Nvidia’s Quadro being more popular, mostly due to Nvidia’s overall popularity with gamers.
Either brand will do a good job for most common CAD uses.
When it comes to the exact model, a low to mid-range card like the Quadro P2200 or the AMD FirePro WX5100 will both deliver for common CAD design uses in manufacturing and architecture. Pair them with a nice, fast i7 or Xeon CPU, 16GB or more of RAM and a nice fast Solid State (SSD) storage drive and you’ll be off and away.
#2 – Brand Name vs Build Your Own
You can go down to the local computer shop and buy a Build Your Own (BYO) computer from a range of manufacturers parts.
In some cases, this will give you the best bang for your buck, especially if your user has good technical skills.
They’ll need good technical skills because by nature, BYO computers are unique. It’s this motherboard, that CPU, this video card, that brand of RAM, this version hard drive.
Because they’re a unique combination of parts, problems are more likely (and these will also be unique). So, the user will need to know what to do if things don’t run smoothly.
On the other side of the highway, brand name systems like those from Lenovo (IBM), HP, or Dell are made in the tens of thousands and the parts and versions of parts are tightly controlled and tested.
This makes running into unexpected problems far less likely. Plus, if there are problems, any decent brand name hardware will come with w 3-year warranty, onsite support and good phone or internet technical support.
If you encounter hardware problems, they will need to be resolved as soon as possible. The BYO option may take weeks or months (or maybe never!) to have pesky issues resolved. So while BYO systems are cheaper, they do come with an increased risk.
#3 – What about Apple?
Apple or MAC computers are very common in video editing, art studios and a range of other creative industries. But are they any good for manufacturing?
In my opinion they can be excellent for CAD work as they are very well built, VERY fast, and look beautiful! But there are some caveats; they are comparatively more expensive, less flexible and upgradable over a 5+ year period and not all manufacturing software will run on them. In my experience, AutoCad will, but REVIT won’t (at least not without using some sort of Windows emulator or dual boot configuration, which kind of defeats the point).
If you love MAC, make sure it will be compatible with the programs you intend to run.
Running a MAC at reception and for the GM or the sales people, should be fine. As I said in the beginning, a mix of technologies is probably best, just make sure you consider the possible limitations Apple MAC hardware and software might bring along for the ride.
#4 – What about Android?
Android devices are becoming more popular in many industries.
When it comes to manufacturing, their range of portable devices that can have custom apps written relatively cheaply for things like QMS software (Quality Management Systems), could be part of an ideal hardware mix.
You’ve got some MAC and PC in design and admin, you’ve got some PC or MacBook laptops and then Android mobile tablets in the warehouse for the QA people to use when doing quality control work. This is not an uncommon situation.
But less complexity is always better, so if at all possible, stick with fewer brands and platforms and you’ll save yourself a few headaches.
#5 – Did someone mention DUST?
One thing common to many manufacturing sites is dust, moisture and heat.
This means the technology you use needs to be resilient, but you also need to make sure you look after it. There’s no point in having a nice new computer in the warehouse if it’s going to get full of dust or cooked in summer.
Keep your hardware in a suitable location, keep it cool, and if dust is unavoidable make sure someone gives it a blast with the air compressor from time to time, to stop it filling up with dust.
If you’re in the manufacturing business, make sure you keep these tips in mind when you’re choosing the right mix of hardware.
The devices you choose will be critical to running your business and if they go down, they will take you with them. Buy smart, protect your equipment and work with your IT provider to help you consider the best mix of hardware for your business.
< Back to News